A couple of years ago I attended a Knife maker's event called a Hammer-in, where I learned how to take black magnetite sand and reduce it into cast iron buttons. These buttons are very high-carbon content (about 4%) and are then forge welded into a bar of wrought iron. This a variation of the Brescian process where you layer up different carbon content steels and repeatedly fold and weld until the carbon content evens out. (more or less)
It starts by reducing the black sand in a crucible placed in a forge of some sort. We used a propane forge. When I say "crucible", I mean a graphite-clay vessel that can withstand the high temps required for this.
These are the crucibles I use.
The charge was about 3 tablespoons of sand and an equal amount of flux. Fluxes come in a variety of forms. Most are a variation of anhydrous borax.
This is placed in the bottom of the crucible.
The blue stuff you see on the crucible is leftover slag glass from a previous melt. The blue color comes from trace amounts of titanium in the sand.
After the crucible has been heated to about 800C, the flux melts and forms a protective layer over the top of the sand. At about 1500C, the sand melts, the iron absorbs carbon from the graphite in the crucible, and the impurities join the flux-glass on top of the charge.
This can be poured out of the crucible into a steel mold or let cool in the crucible to be removed later. Either way, the small button of cast iron comes out with a layer of glass-like substance over the top.
This gets removed by tapping with a hammer to reveal the button.
So, you make a bunch of these and now comes the fun part.
Take a piece of wrought iron. These can be difficult to find, but there are still some old wagon wheels and other pieces out there laying in fields or stuffed in someone's barn.
Bring the iron up to a red heat and start to fold it. Lay the button on one side of the fold.
Heat that up until the button starts to melt. The really high carbon content lowers the melting point considerably. This will start to melt around 1200C. At this point, you can spread the button like peanut butter and complete the fold to encase the cast like a sandwich. Fold down the edges a little so the cast iron doesn't spew out the sides during the next step. Flux the bar and heat it to welding temp, that's roughly 1340C or when the flux starts to boil, whichever comes first. Hammer the bar down to complete the forge weld.
Draw it out to a flat bar again, start the fold, add another button, and repeat as desired. Eventually, you decide you are done and should have a bar of high carbon content steel.
This bar has 7 buttons folded into it and is roughly 250 layers. I forged a small knife blade out of this.
After grinding, sanding, and etching in ferric chloride, the blade looks like this.
The finished knife and sheath.
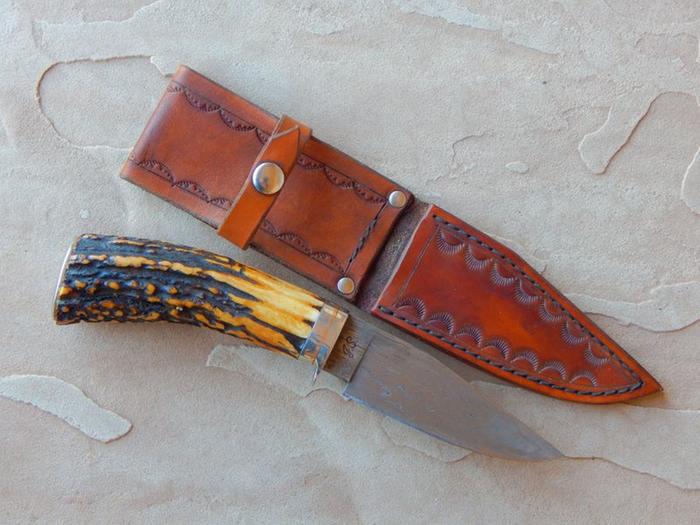